New Capability! Now Offering Stainless Steel Laser Cutting Services
Lake Forest, CA - Do you have a bracket, trim, badge, or similar project you’d like to explore in precision cut 304 brushed or polished stainless steel? Don’t have the time or budget to invest up front in tooling? Camisasca Automotive Manufacturing, Inc. now offers an in-house solution for you!
While Camisasca Automotive Manufacturing, Inc. has long been an established staple of the automotive industry, providing reliable quality products and customer service for their foundation license plate frames and related stainless steel accessories, we are no stranger to innovation. First to utilize architectural grade #8 polished stainless steel in place of chrome license plate frames, first to market with an OE logo valve stem cap, holder of (5) unique utility and design patents; with a career spanning over four decades the list goes on…
Recently, as a second-generation US family-owned organization, succession planning and implementation has revitalized our drive to differentiate the brand through additional knowledge and capability. Founder son, Colin Camisasca-President and daughter, Marisa Camisasca-Vice President are eager to carry the baton of innovation, rather than rest on their laurels.
Enter the Mitsubishi SR-F Fiber Laser - so when it came time to reinvest in our in-house metal stamping division, management took the opportunity to strategically position the business. While traditional presses and stamping are confined to the capabilities of dies and expensive up-front tooling, Fiber Laser technology has come a long way in providing not only simplification of set up, but also augmented throughput and material utilization. When comparing the new process to those of a traditional metal stamp set up; the benefits became clear:
Ability to cut intricate shapes and sizes up to 48” x 64” in 18 or 20ga stainless steel from standard size sheet stock without the need for expensive stamping dies.
Efficient in supporting both low and high-volume production, with ability to integrate a product mix within singular runs.
Automated production programming with less operator involvement, more safety, and less room for error.
Maximum material utilization to minimize the costs of waste while meeting sustainability targets.
*Available secondary process to provide a fully finished product: brake press, polishing, media blasting, deburring, laser etching, adhesive application, powder coat and PVD finishing, and light assembly.








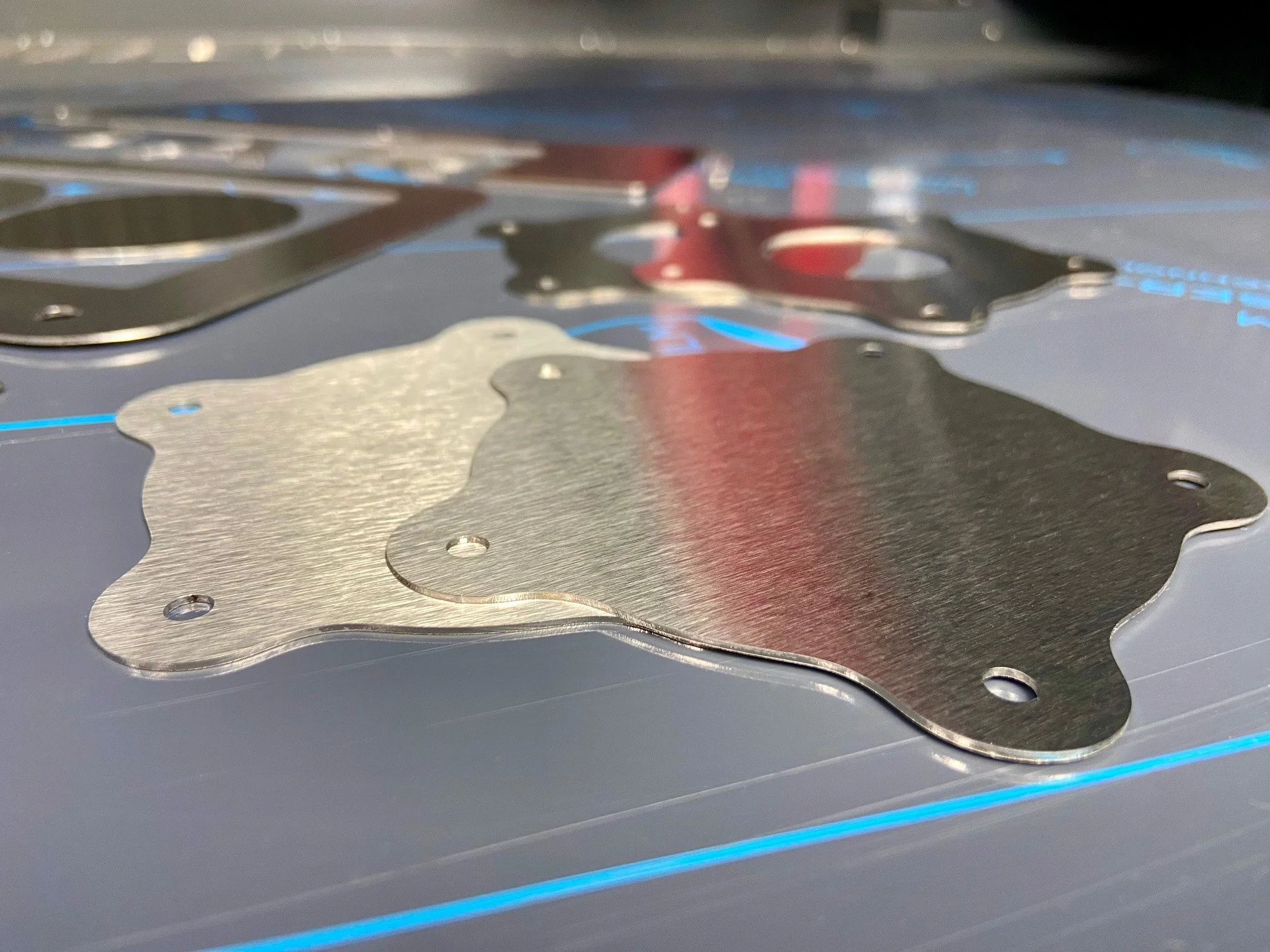


Considerations began in 2019 as CAMI cautiously explored the capabilities of the new process. While it was important for us to expand our services, it was essential for the process to support our foundation product lines of license plate frames, marque plates, plate mounting brackets, and keychains. Please reach out with questions or concerns on your existing parts.
After extensive testing, training, and research, our top of the line Mitsubishi SR-F Fiber Laser was installed and facility upgraded to support this new process in November 2021. This included a new German made ARKU Edge Breaker for deburring of complex laser-cut shapes and a 3000L Nitrogen Tank for superior cut cooling. Subsequently the entire process was brought online in January 2023 and after many months of testing and perfecting, has just met its safe launch criteria in Q2 2024.
During this time, CAMI was able to explore and leverage the new no-tooling capabilities to launch two new products; the Electronic EPlate Frame for Reviver® Plates – first to market with patent pending design - and the Inhouse Medallion Keychain – with improved pricing and additional build options. In a time of heightened personalization and swift development, CAMI is proving the new investment has what it takes to support our customers’ needs.
So what will you develop? Contact CAMI today and our sales and engineering team will be glad to explore the possibilities of your project. Or visit our website at www.camincusa.com to explore past projects. Since 1982, CAMI has been bringing bespoke product ideas to life in both short run and long run production programs for OE and aftermarket customers in the US and beyond.
*All images and video above taken on normal production days, no special planning or cleaning has taken place. Come visit our showroom style plant today!